Choosing Between Laser Cutting & Water Jet Cutting: A Guide for Engineers & Designers
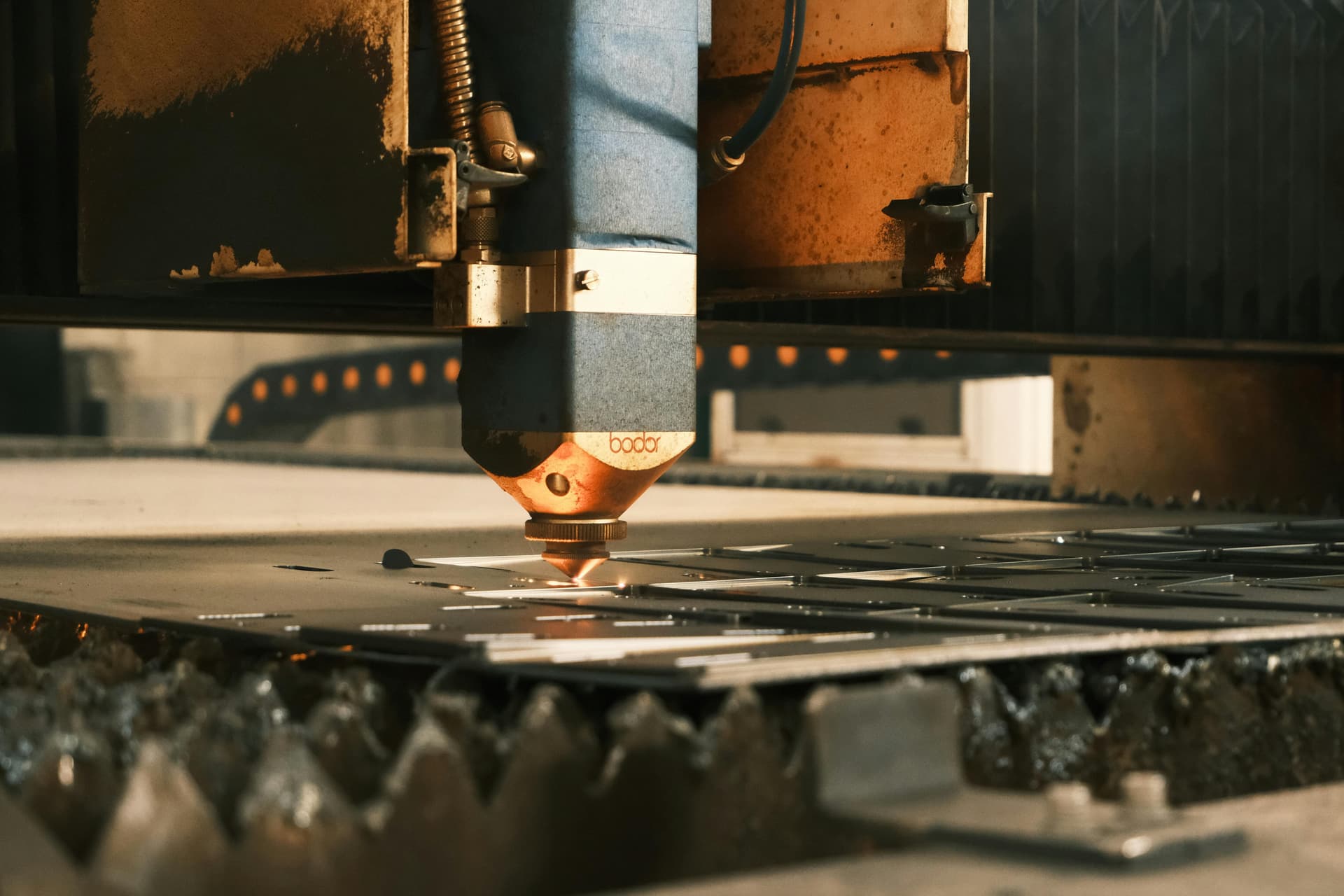
When working on sheet metal prototyping or custom metal fabrication in the San Francisco Bay Area, choosing between laser cutting vs water jet cutting is crucial. Each method has strengths and weaknesses, depending on material type, thickness, precision needs, and budget. This guide breaks down the key differences and best use cases for each process, helping engineers and designers in Oakland, San Francisco, and Silicon Valley make informed decisions.
Key Differences Between Laser Cutting & Water Jet Cutting
1. Precision & Accuracy
- Laser Cutting: Extremely precise, with tolerances around ±0.005 inches (0.13 mm) and a kerf width as small as 0.006 inches (0.15 mm) . Ideal for intricate details and sharp corners.
- Water Jet Cutting: Can achieve tolerances of ±0.02 inches (0.5 mm) . Less precise than lasers but does not introduce a heat-affected zone (HAZ), making it suitable for materials that may warp under heat .
2. Material Compatibility
- Laser Cutting: Works well with metals, plastics, wood, and fabrics but struggles with reflective metals (e.g., brass, copper) and materials that produce toxic fumes (e.g., PVC).
- Water Jet Cutting: Cuts virtually any material, including metals, glass, stone, ceramics, rubber, and composites . It is heat-free, making it ideal for delicate or thick materials .
3. Cost & Efficiency
- Laser Cutting: Faster for thin to medium thickness materials (up to 0.5 inches), reducing per-part cost . Requires minimal post-processing .
- Water Jet Cutting: Slower but excels at thicker materials (up to 8+ inches) . Higher consumable costs (abrasive materials) but avoids the need for secondary finishing .
When to Use Laser Cutting vs Water Jet Cutting
Use Laser Cutting If:
- Your material is thin to medium thickness metal (e.g., stainless steel, aluminum, mild steel).
- You need intricate cuts with fine details and high precision .
- Speed and high-volume production are priorities .
- Your part needs minimal post-processing .
Use Water Jet Cutting If:
- Your material is thicker than 0.5 inches or is difficult to cut with a laser .
- You need to cut glass, stone, ceramics, composites, rubber, or mixed materials .
- You want to avoid heat distortion or a heat-affected zone .
- Your part requires a clean, smooth edge with no burning or melting .
Industry Applications in the Bay Area
Aerospace
The Silicon Valley aerospace industry relies on precision cutting for advanced materials.
- Water Jet Cutting: Used for titanium airframe components and jet engine turbine blades to avoid heat-related micro-cracks .
- Laser Cutting: Suitable for thin sheet metal parts and brackets where heat effects are not a concern .
Automotive & EV Manufacturing
With the rise of electric vehicles (EVs) in the Bay Area, precision cutting is essential for rapid prototyping and production.
- Laser Cutting: Used for sheet metal body panels, precision brackets, and exhaust components due to speed and automation .
- Water Jet Cutting: Applied to custom automotive gaskets, thick chassis parts, and carbon fiber components .
Architecture & Design in Oakland & San Francisco
High-end architectural metalwork and design firms in San Francisco and Oakland use both cutting methods for building facades and artistic elements.
- Water Jet Cutting: Ideal for decorative metal panels, stone inlays, and custom signage .
- Laser Cutting: Used for intricate patterns in metal facades, acrylic, and wood designs .
Cost Considerations in the Bay Area
Laser Cutting Costs
- Lower cost per part for thin materials due to faster cutting speeds .
- Higher machine cost but fewer consumables (mainly assist gases like nitrogen or oxygen) .
- Minimal post-processing reduces total production cost .
Water Jet Cutting Costs
- Higher consumable costs due to abrasive material usage .
- More maintenance required (high-pressure pumps and nozzles wear out faster) .
- Better suited for low-volume, high-precision jobs and materials where lasers cannot be used .
Conclusion
Choosing the right cutting method depends on your material type, thickness, precision needs, and budget.
- Laser Cutting is best for thin metal parts, intricate designs, and high-speed production .
- Water Jet Cutting is preferred for thicker materials, heat-sensitive materials, and a wider range of material types .
For most projects, consulting a Bay Area fabrication shop that offers both services can help determine the best method based on quality, speed, and cost. Whether you're in Oakland, San Francisco, or Silicon Valley, local cutting services can provide tailored solutions for your specific needs.